Understanding Extrusion Moulding: A Comprehensive Guide
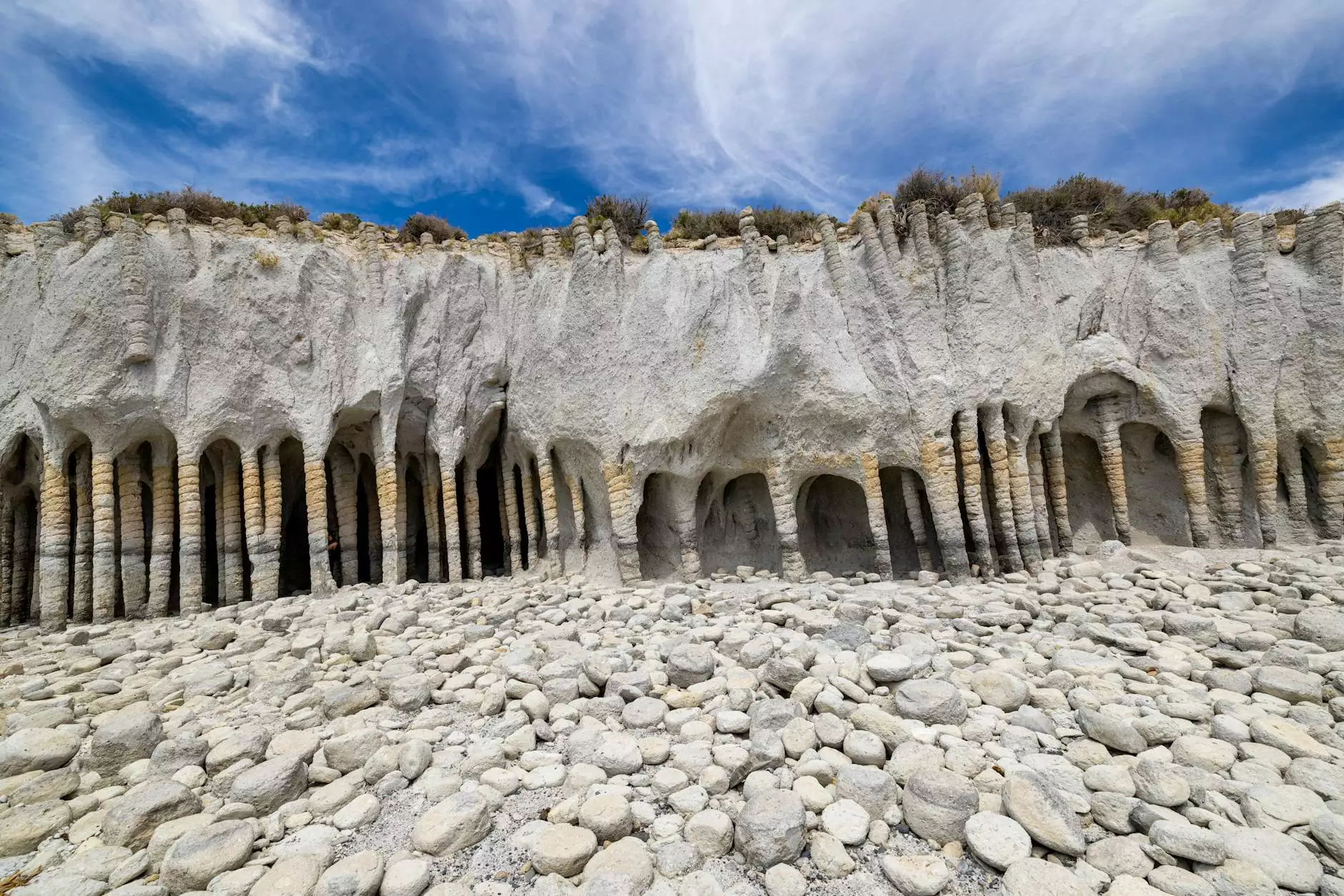
Extrusion moulding is a crucial manufacturing process used to create a vast variety of products, from simple plastic components to complex shapes. This article delves deeply into the nuances of this process, its applications within the domains of art supplies, product design, and 3D printing, while providing valuable insights for businesses operating in these spaces.
What is Extrusion Moulding?
At its core, extrusion moulding is a method where materials are transformed into specific shapes by forcing them through a die. The process begins with raw materials, such as thermoplastics, which are heated and pushed through a specifically designed die to form a continuous profile. After it emerges from the die, the newly formed shape is cooled and cut into the desired lengths.
The Process of Extrusion Moulding
The manufacturing process of extrusion moulding can be broken down into several key stages:
- Feeding: Raw materials are fed into a heated barrel where the material begins to melt.
- Extrusion: The melted material is forced through a die, shaping it into a continuous profile.
- Cooling: The extruded material cools and solidifies into its final form.
- Cutting: The solidified product is cut into lengths as per design requirements.
Applications of Extrusion Moulding
Extrusion moulding has a wide range of applications across various industries. Below, we highlight a few key sectors where this process plays a pivotal role:
1. Art Supplies
In the realm of art supplies, extrusion moulding is used to produce various essential products such as:
- Colored Crayons: The vibrant colors and consistency achieved through extrusion make it perfect for crafting crayons.
- Markers: The ink reservoir tubes in markers often utilize extrusion moulding for precise shapes and wall thickness.
- Glue Sticks: The uniformity in glue sticks is achieved through the extrusion process, ensuring smooth application.
2. Product Design
Product design heavily benefits from extrusion moulding due to its capability for creating custom shapes and profiles. Some notable uses include:
- Custom Plastic Profiles: Businesses can produce unique profiles tailored to their specific needs.
- Prototyping: The extrusion process allows for rapid prototyping, enabling designers to iterate quickly.
- Functional Parts: Many functional parts for electronic devices and appliances are made using extrusion techniques.
3. 3D Printing
The intersection of extrusion moulding and 3D printing technology has unleashed innovative potential:
- Filament Production: The production of plastic filaments for 3D printing often uses the extrusion process.
- Increased Material Variety: Various materials can be extruded to create filaments with different properties and applications.
- Rapid Production: This synergy allows for faster production rates in 3D printing applications.
Benefits of Extrusion Moulding
The adoption of extrusion moulding offers numerous advantages for businesses seeking to enhance their manufacturing capabilities:
- Cost-Effectiveness: The extrusion process is continuous, which generally makes it more economical for large production runs.
- Material Efficiency: Extrusion creates minimal waste, with the ability to recycle leftover materials.
- Versatility: The process can accommodate a wide range of materials and shapes, giving designers greater freedom.
- Quality Control: The consistency and precision of extruded products enhance quality assurance processes.
Challenges in Extrusion Moulding
Despite its advantages, extrusion moulding comes with its own set of challenges. Understanding these can help businesses better navigate potential issues:
- Machine Maintenance: Keeping extrusion equipment in optimal condition is crucial and can be resource-intensive.
- Material Limitations: Not all materials are suitable for extrusion; thus, choices may be limited.
- Initial Setup Costs: The cost of setting up extrusion moulding equipment can be high, depending on the complexity of the product.
Future Trends in Extrusion Moulding
As technology evolves, extrusion moulding adapts and grows, paving the way for exciting opportunities:
- Smart Materials: The incorporation of smart materials into extrusion processes is on the rise, allowing for responsive products.
- Sustainability Initiatives: With increasing emphasis on sustainability, companies are seeking eco-friendly materials and practices in extrusion.
- Automation: Enhanced automation in extrusion lines increases efficiency and reduces labor costs, shaping the future of the industry.
How to Optimize Your Business with Extrusion Moulding
For businesses in art supplies, product design, and 3D printing, leveraging extrusion moulding effectively can provide a competitive edge. Here are some strategies to consider:
1. Invest in Quality Equipment
High-quality machines yield better results and increase production efficiency. Investing in updated technology can significantly enhance output quality.
2. Focus on Research and Development
Innovating through R&D can create unique products that set you apart from the competition. Test new materials and shapes to explore new market opportunities.
3. Collaborate with Experts
Partner with specialists in extrusion moulding to optimize processes and troubleshoot manufacturing challenges. Collaboration can lead to improved technologically advanced solutions.
4. Embrace Sustainability
Consumers increasingly prefer companies that prioritize eco-friendliness. Consider using recycled materials and developing sustainable practices to attract a broader audience.
Conclusion
In summary, extrusion moulding is not just an industrial process but a transformative technique that underpins many products in the art supplies, product design, and 3D printing sectors. By understanding its intricacies, leveraging its advantages, and navigating its challenges, businesses can harness the full potential of this technology. Staying informed about future trends and adopting a proactive approach will undoubtedly help companies thrive in this dynamic landscape. Embrace the power of extrusion moulding and elevate your business to new heights!