The Essential Guide to **Pressure Die Casting Tools**
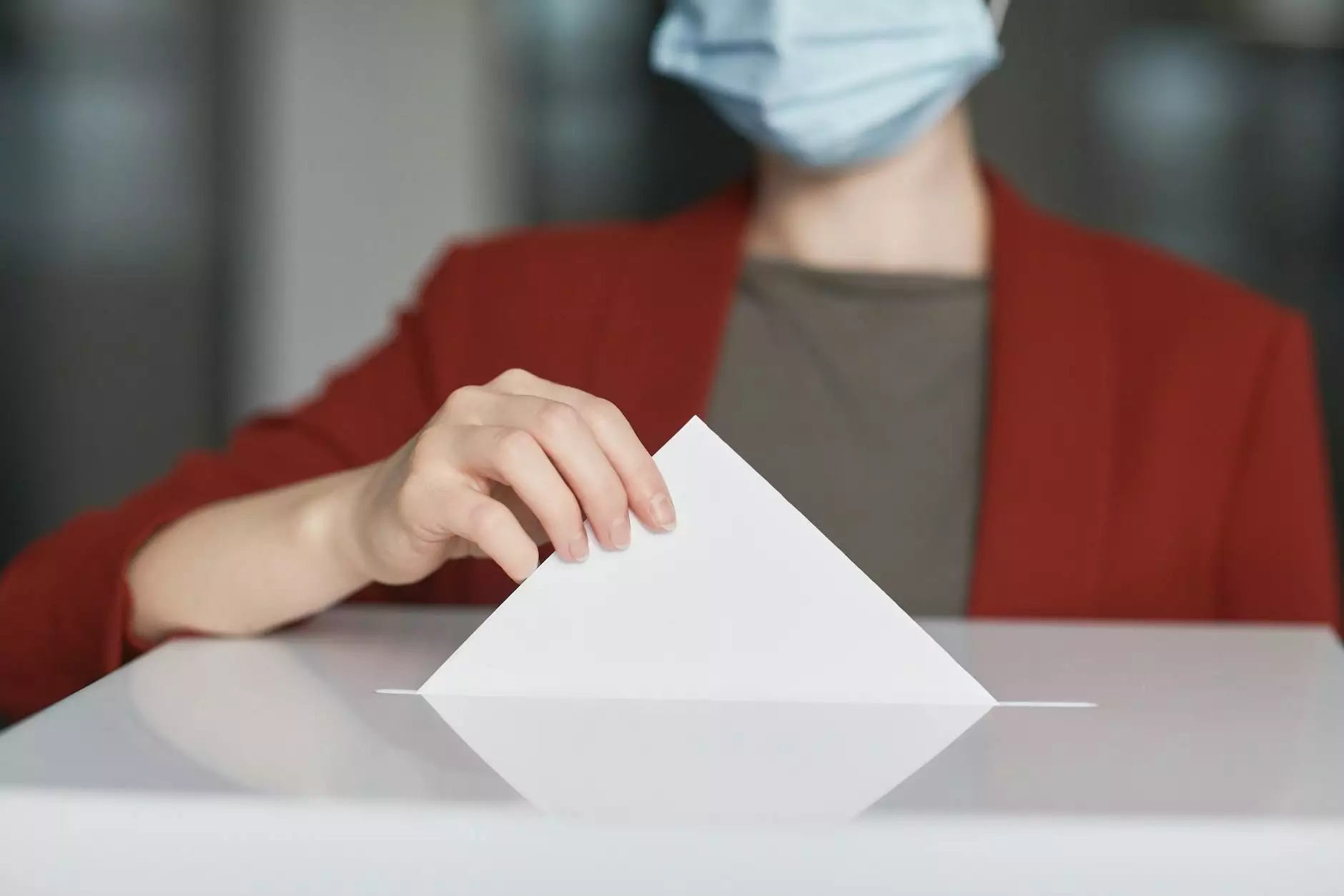
In the realm of modern manufacturing, pressure die casting tools play a pivotal role. They allow for precision, efficiency, and exceptional quality in the production of metal components. This extensive article delves into the nuances of pressure die casting tools, exploring their operation, advantages, applications, and selecting the right tools for your business needs.
Understanding Pressure Die Casting
Pressure die casting is a manufacturing process that involves forcing molten metal under high pressure into reusable molds. This technique is ideally suited for producing complex shapes and high volumes, making it a favorite in industries such as automotive, aerospace, and electronics.
How Pressure Die Casting Works
The process of pressure die casting can be broken down into several critical steps:
- Melt Preparation: Raw metal is heated in a furnace until it reaches a molten state.
- Injection: The molten metal is then injected into a mold under high pressure, ensuring that every cavity is filled accurately.
- Cooling: The metal is allowed to cool and solidify, forming the desired shape.
- Mold Removal: Once solidified, the mold is opened, and the cast part is removed.
- Finishing: After removal, the cast parts may require additional machining or finishing processes to achieve tight tolerances or surface finishes.
Benefits of Using Pressure Die Casting Tools
The adoption of pressure die casting tools comes with numerous benefits:
- High Production Speed: The process can produce large quantities quickly due to the efficiency of the repeatable die casting method.
- Dimensional Accuracy: The use of hardened steel molds enables very precise and detailed shapes, reducing the need for secondary machining.
- Complex Geometry: Designers can create intricate designs that may be challenging or impossible with other manufacturing methods.
- Material Versatility: A wide variety of metals, including aluminum, magnesium, and zinc, can be used in the pressure die casting process.
- Reduced Waste: The efficiency of the process ensures minimal waste, as excess metal can often be recycled and reused.
Applications of Pressure Die Casting Tools
Pressure die casting tools have vast applications across various industries:
1. Automotive Industry
The automotive sector is one of the largest users of pressure die casting tools. They are utilized to produce components such as:
- Engine components
- Transmission housings
- Structural parts
- Wheel rims
2. Electrical Industry
Electrical components often require exact dimensions for functionality. Pressure die casting tools are used to create:
- Electrical housings
- Connectors
- Heat sinks
3. Aerospace Industry
The aerospace industry demands high specifications, and pressure die casting tools meet these needs by producing lightweight and durable parts such as:
- Airframe structures
- Brackets
- Fasteners
Selecting the Right Pressure Die Casting Tools
Choosing the right die casting tools is vital for the success of your manufacturing process. Here are some key factors to consider:
1. Material Considerations
The choice of materials affects the performance and durability of your casting. Common materials include:
- Aluminum alloys for lightweight applications
- Zinc alloys for high detail and low-cost parts
- Magnesium alloys for applications requiring high strength-to-weight ratios
2. Tooling Quality
High-quality tooling will improve the longevity and efficiency of the die casting process. Consider:
- The hardness and heat treatment of the die materials
- The precision of machining
- Design features that facilitate airflow and cooling
3. Production Volume
Assess your production volume needs to determine the type of die casting tooling required. For high-volume production, invest in robust tooling solutions.
Common Challenges in Pressure Die Casting
While pressure die casting tools offer many benefits, there are also challenges to consider:
1. Porosity
This refers to the presence of tiny air pockets in cast parts that can weaken their mechanical properties. Techniques to minimize porosity include:
- Optimizing injection speed
- Reducing metal temperature discrepancies
- Improving mold design for better evacuation of trapped air
2. Tool Wear
Due to the high-pressure nature of the process, tools can suffer wear and tear. Regular maintenance and choosing high-quality materials can mitigate these issues.
3. Temperature Control
Maintaining the right temperature during casting is critical for high-quality output. Implementing robust temperature monitoring systems can help manage this aspect effectively.
The Future of Pressure Die Casting Tools
As technology evolves, so do the tools and methods used in pressure die casting. Emerging trends include:
1. Automation and Robotics
Incorporating automation can enhance efficiency and reduce labor costs, allowing for:
- More consistent quality
- Reduced lead times
- Increased production speeds
2. Advanced Materials
Research into new alloys and composite materials may lead to innovations that improve the performance of die-cast parts.
3. Sustainable Practices
As industries pivot towards sustainability, pressure die casting can become more eco-friendly through:
- Reducing energy consumption
- Implementing recycling of excess materials
- Utilizing biodegradable cooling agents
Conclusion
The significance of pressure die casting tools in modern manufacturing cannot be overstated. Their ability to produce high-quality, complex components at scale makes them indispensable in many industries. By understanding the intricacies of the process, the benefits of using these tools, and how to overcome common challenges, manufacturers can effectively leverage pressure die casting to drive efficiency and quality in their operations.
For businesses keen on optimizing their manufacturing processes, investing in high-quality pressure die casting tools is essential. By collaborating with experienced suppliers and keeping abreast of technological advancements, companies can secure a competitive edge in their respective markets.